October and November have been somewhat slow and lonely at TLG. Jack and I finished a thorough cleaning of the bare Mustang unibody after having stripped all the paint from the body and we acid-etched the carcass for basic metal preservation and rust prevention while we go through the next few prep steps.
And that’s when Jack’s cross-country season and college applications kicked in…
While I’m glad Jack has his priorities in the proper order, I’m not spending as much time in the garage now that Jack’s been really busy. I will be back in the garage the 2nd week of December to get the Mustang seams “leaded” and perhaps even replace the rear quarter panels while Jack’s busy with other (more important) activities.
I hope he is pleasantly surprised with the progess when he comes up for air.
In other exciting news: Three Lions Garage has its first British occupant on the way since we sold the ’55 Elva and ’35 Morgan three wheeler. While visiting the Classic Motor Show at the 2,000,000 square foot National Expo Centre Birmingham two weeks ago I met several interesting groups of like-minded gearheads. The show is the largest classic auto event in the UK and it’s safe to say it’s BIGGER THAN HUGE! I can’t accurately describe how big it is other than to tell you that I ended up walking 9 miles (!) in about 6 hours at the show.
I browsed the vendors section (in which they were selling everything new and used related to classic cars) and met with fellow members of the Citroen Car Club ltd, the 2CV club and the Messerschmitt Owners Club. I took the opportunity to visit with Andy at the stall rented by Hortons Books, my absolute favorite rare and new automotive book dealer, run by Ben Horton and his wife Jennifer. I found some mirrors for the ’27 Rally and also procured some hurricane hats and goggles for Jack and me to use in the upcoming California Mille. But I digress…
Near the end of my visit I saw three beautiful vintage Land Rovers owned by members of the Birmingham Land Rover Group, a motley crew of spirited Land Rover enthusiasts. They couldn’t have been more friendly and were quite a fun bunch. I started speaking with one of their members, a retired R&D engineer at Land Rover and within an hour I was the proud new owner of a 1978 Land Rover Series 3 Safari edition 109 Estate. This acquisition solved my “holiday gift for Linda” conundrum. She will be ecstatic—or so I hope…

business end of Linda’s holiday gift
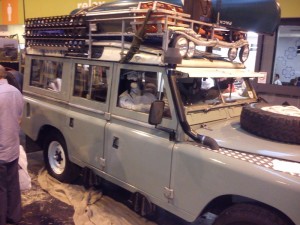
crash dummy and canoe not included
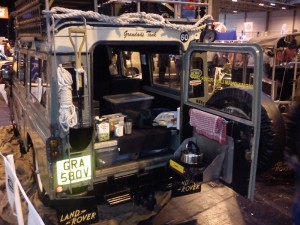
Grandad’s Tank
This multiple-award-winning car has only 38,000 original miles on the odometer, is fully loaded with every available option and was sold fully “kitted out” with all the bits shown (including roof rack, sand ladders, jerry cans and spare water tank) but sans canoe. Even more desirable is that this vehicle has been under the loving care of a very talented retired Land Rover engineer, and getting to know Ken has been the most enjoyable element of the entire experience.
Linda’s “new” car sailed from Southampton, UK on a roll-on/roll-off vessel which is due in Port Hueneme, CA at the end of this month. I can hardly contain my excitement.
Filed in Restoration Log | Tagged: 1969, 2CV, automobile, Automotive, Birmingham, Birminham Land Rover Group, BLRG, California Mille, Captain, Citroen, classic car, Classic Motor Show, College Applications, Cross Country Team, Fastback, Father and Son, Garage, Horton's Books, Land Rover, Mille Miglia, Mustang, National Exposition Centre, NEC, parts, Port Hueneme, project, Restoration, Southampton, Three Lions Garage, TLG, unibody, Varsity, Wallenius, workshop